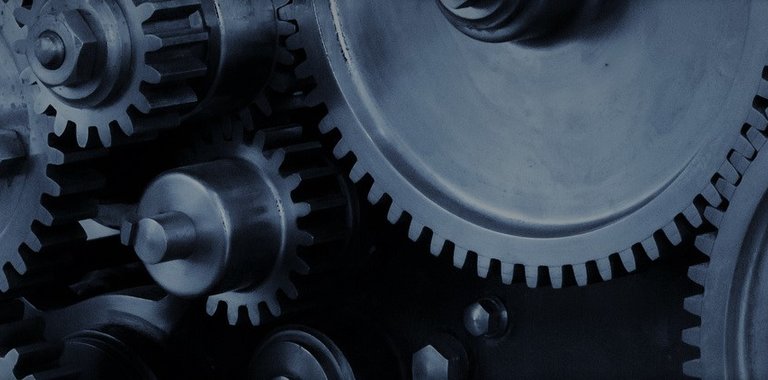
Monitoring Gearboxes
Gearboxes (GB) are used to change machine shaft speeds and torque or to change rotational axis direction. The condition and longevity of a GB is usually of interest to end users to provide continuous plant operation. Thus, condition monitoring of GB is very common practice.
Quality of the mesh has a strong influence on the lifetime of the GB. The alignment and fit of the mesh is very sensitive to the parallel, axial, and angular positions of the shafts. Assuming the gears have been designed properly and manufactured correctly, mesh problems will be caused by other root cause problems in the system. It is important to remember that the gearbox system is imbedded in an extended system that includes the driving machine, the driven machine, couplings, the foundation, any piping attached to the gearbox casing, and the oil supply system. The complexity of interrelationships among these components requires a comprehensive monitoring system that can address the effects of these components. The objective of a gearbox monitoring system is to provide enough information to both monitor the existing state of the machine and to enable diagnosis of root cause problems.
This Orbit article gives some recommendations we have for GB monitoring. A more comprehensive description can be found from our application guide for GB that is available from Your local Bently Nevada (BN) sales manager.
By far the most common condition monitoring method for GB is vibration, as is the case for all rotating assets. On top of that, significant additional value may be gained by monitoring oil condition and oil particles (ferrography), as well as bearing temperatures. In this article we will just take a look at the vibration part.
The design of a GB sets some fundamental criteria for the condition monitoring, both for sensor and monitoring point of view. There are a large number of different GBs out there but most can be divided into one of the three following classes:
- High speed GB with journal bearings
- Low speed GB with relative simple design and with rolling element bearings (REB)
- Low speed GB with complex design, often with planetary stage(s)
Gear teeth meshing will create vibrations that are used to analyze the condition of a GB. It is important to understand that, unlike rolling element bearing failure frequencies, gear mesh frequencies (GMF) are present when the GB is in perfect condition. These include GMF (#of teeth x speed of the shaft) and its harmonics, along with the running speed sidebands of both shafts in the mesh. When a GB starts to fail, the amplitudes of GMF and its harmonics will change, as well as the amplitudes of the sideband frequencies. Without knowing these frequencies, GB condition monitoring will be challenging. This information is vital also on high speed applications where it is not always easy to find an accelerometer meeting the linear frequency range general rule of 3,25 x GMF.
It must be noticed that GMF is not the only frequency of interest when evaluating GB condition. Other frequencies of interest are tooth repeat frequency and assembly phase passage frequency. Please refer to BN GB application guide for more detailed information of these. And, in presence of REBs, obviously their faulty frequencies must be known.
BN recommendation for GB transducer suite is to have proximity probe pair installed for each journal and thrust bearing and three accelerometers in suitable places on the casing, taking measurements on horizontal, vertical, and axial directions. On top of that, each shaft should be equipped with a keyphasor (KP). If this is not possible, or considered to be too expensive, then the minimum instrumentation contains proximity probe pair installed on the input shaft and output shaft bearings. And a single accelerometer is the minimum.
并不少见,GMF高速GBin the range of 5000 Hz or above. In this case, fulfilling the 3,25 x GMF linear range requirement may be challenging, and it is not uncommon to settle for something like 2,25 x GMF. Contact Your local BN sales manager to discuss the options we have.
The sensor suite above will give a good set of condition monitoring data:
XY pair:
- Orbit to evaluate journal bearing condition
- Orbit to evaluate shaft unbalance situation
- Shaft position to evaluate alignment situation, both GB internal and external
Accelerometers:
- Acceleration data to evaluate gear mesh
- Acceleration data to evaluate gear loading
- Velocity data to evaluate unbalance, misalignment and looseness
- BN patented Side Band Energy Ratio (SER) will help detecting changes in the mesh
这个单级减速阶段GB是仪器的交流cording BN recommendation, so XY proximity probe pair on each bearing and three accelerometers on the GB casing. The first symptom showing a problem was increased vibration, both in acceleration and velocity. This was followed by increase of shaft vibration, especially on the blind end of the high speed shaft. A detailed analysis gave reason to believe that at least two teeth of the pinion have failed. The machine was stopped and, indeed, several teeth on the pinion had failed, and lost of material was on the blind end, see Figure 2.
This GB has no vibration instrument and we do routine data collection with portable Scout instrument. The first time the data was collected we noticed quite high impact seen on the acceleration waveform. The impact seemed to take place once per revolution. A time synchronous averaged data was collected in order to gain a higher confidence of the issue. This clearly showed single teeth were impacting when entering the mesh. On the next overhaul GB was opened and it was found that one tooth end had a different profile from the others.
To monitor teeth condition properly, one accelerometer is recommended for each gear stage. Additionally, at least one accelerometer mounted in the axial direction is recommended. More accelerometers are required if REB failures are not covered with above set of sensors. Less number of sensors will likely make it challenging to monitor all failure modes properly. Shaft speed information is vital on this case too, but it may not be necessary to have a dedicated sensor for it if speed info. can be gained digitally from the control system or if GB is running on constant speed.
The sensor suite above will give a good set of condition monitoring data:
Accelerometers:
- Acceleration data to evaluate gear mesh and REB failures
- Acceleration data to evaluate gear loading
- Velocity data to evaluate unbalance, misalignment and looseness
- Demodulation data to evaluate REB failures
- BN patented Side Band Energy Ratio (SER) will help detecting changes in the mesh
Power plant has two main cooling pumps. After summer overhaul it was noticed by using portable instrument that the vibration in GB has increased from ~4 mm/s rms to ~ 14. The only changed spectral component was GMF. The waveform was very clean with Creast factor 1.90, so no impacting was present. It was concluded something has changed in the way teeth mesh against each other. That something was found when oil analysis was done, showing way too much water in the oil. Changing the oil returned the vibration level to normal.
Ethylene plant has four seawater pumps, all equipped with BN 1900/65A monitors and multiple accelerometers. After an overhaul high frequency acceleration values started to increase on one of the GB, while velocity readings remained stable, figure 4. Additional analysis was performed with portable instrument and this showed symptoms of REB failure on GB high speed shaft. After trending the situation for a couple of months GB was overhauled and failed bearing was replaced.
When dealing with a complicated GB with several reduction stages, or a planetary type design, there will be a lot of mesh frequencies and multiple sidebands in the spectrum and, on top of that, other excitation frequencies. Often, structural natural frequencies will also be present due to impact-type excitation and friction forces. It is necessary to know all these frequencies if a GB failure - its severity and location - is to be pinpointed. A typical example of this kind of GB is the ones used on wind turbines. Very slow speed GB can be found also in many industrial applications, like pulp, paper, steel, and chemical industries.
The sensor suite and analysis methods are not necessarily any different from low speed GB with simple design. But, the spectral data does not necessarily give enough information for pinpointing a problem, waveforms of both acceleration and demodulation may turn to be more helpful.
A significant step change on vibration trend was observed on GB, figure 5, using BN Wind.Adapt monitoring system. The spacing of the impacts suggested problem on an intermediate shaft. A borescope inspection confirmed this, by showing a broken tooth.
A pulp mill mixer is driven by an electric motor and four stage GB with output about 6 rpm. System is instrumented with several accelerometers and System1 condition monitoring SW.
在改革搅拌机叶片洗一个d after the unit was put back in operation the vibration values started to slowly increase. Condition monitoring group investigated the issue and finally came to conclusion that mixer is rotating into the wrong direction. The washing process required rotation into both directions and by human error, the wrong direction was left on. Not only does the mixer work less effective but also there is a high risk of damaging GB as it is designed to operate only to one direction.
Bently Nevada has a wide selection of different monitoring instruments for GB monitoring. Depending on many aspects like criticality of the machine train, driver and driven machine, process and speed variation, protection need, number and type of used sensor, the best choice may be any of the above instruments.
Contact your local BN sales manager to find out how we can fulfill your monitoring need for Gearboxes.
Petri NohynekField Application Engineer Bently Nevada Digital Solutions Baker Hughes