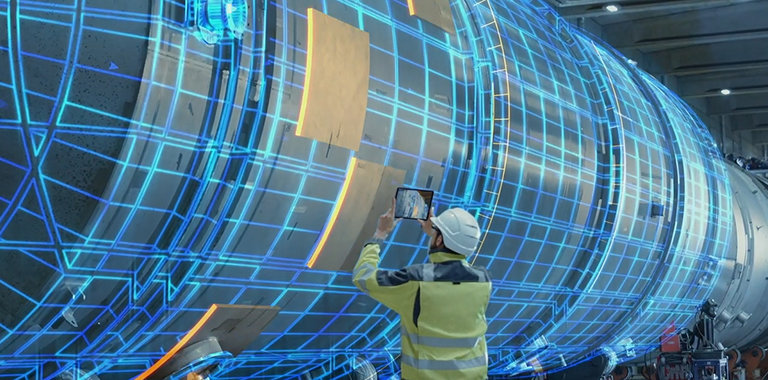
People’s Corner: The Machinery Diagnostics Services Team Interview with Pamela Litka & Nicolas Peton
From a single engineer in 1972, ourMDS capabilities已经包含一组~ 150专用professionals today, many with decades of experience. We have completed more than 18,000 machinery diagnostic projects and the results are maintained in an extensive archive so that lessons learned on one project benefit other projects where similar machinery problems are encountered. Our sophisticated IT capabilities allow MDS colleagues from around the world to easily collaborate in real time using this archive and their collective areas of expertise. This ensures that our extensive knowledge and broad experience can be brought to bear on each problem, regardless of where the machinery is located.
Nicolas, please tell me about yourself. (favorites, growing up, etc.)
I was born in Brittany (northwest France) but I have spent a lot of time over the years living outside of France. While studying my “Diplome d’ingénieur” I spent one year at the Politecnico di Milano (Italy) and then one year at the Technical University of Berlin (Germany). After that I did my military service (16 months) for the French foreign office in Israel at the Technion. It was during my studies that I started to visit and live in new places and quickly found I have a love of travel, something I still enjoy today. I do like foreign languages and I read a lot of books (History and Science mainly) and loved comics. Today I have a house in Bordeaux (southwest of France) where I live with my son, Yuri. At home I have a full lab with Rotor Kit, Racks, servers, computers…!
Can you tell us about your career history with Bently Nevada, etc.?
I received my Diplome d’Ingénieur in Mechanical Engineering in 1997 and my Ph.D. degree in Mechanical Engineering in 2020, both from the Université de Technologie de Compiègne (France). I have been working for Bently Nevada of Baker Hughes since 2006 in the Machinery Diagnostic Services group. I am currently Global Director for the Bently Nevada Machinery Diagnostics Services. Previously I worked for two different manufacturers (Alstom Steam turbine and Cryostar expander/compressor) where I was a lead commissioning engineer in charge of site start up activities, a role that took me worldwide. I also worked as an operation and maintenance engineer in the chemical industry (PPG industry, USA) and as freelance for startup activities worldwide. I have also been a mechanical/acoustical research engineer in research institutes (Technion, Haifa and TU Berlin). I am a member of the Pump Symposium committee and have been the author of several papers published and presented at the international conferences.
Please share with us your evolving role with BN MDS and how it differs from your previous role(s).
In fact, at Bently I have always been an MDS. I was hired as an MDS in 2006, became Tech Lead for southern/western Europe in 2011 and then MDs Global Director in 2015. I do not see myself outside of MDS!
What are the take-aways from your previous role(s) that you have brought into your role?
I have always worked in the field of rotating machines and my experiences as a commissioning/startup engineer for ST, GT, compressors, Pump, LNG plants, BOP, and Air separation units are helping me to “tune” the team to really look at all the data to solve/monitor machines.
Who is your team comprised of?
Today, within MDS there are about 170 engineers globally. Among them are 17 technical leaders that are reporting to me.
It’s very impressive, the years of experience represented in your team. What do you attribute the success of such an experienced team to?
The total cumulated experience time of theMDS工程师在BN大约是1400年的经过nce. Many of them also have past experiences from other companies (OEM, end users, etc.). The academic level is also very good (Bachelor, Master, PhD). All of those engineers have always worked around rotating machines but more importantly I hope they all have a passion for this type of diagnostic work. It is that interest in the work that has kept many of us within the MDS team. I think MDS (since 1972) is unique, as it is a service team within a company responsible for creating and manufacturing the tools that we, as an MDS team, use daily. This gives us, as a services team, an advantage; as we can access and directly feedback into the engineering side of the business. This symbiotic relationship between the MDS group and product development has been significant in our long-term success and has been part of the way we work since MDS started.
Trusting relationships between customers and the MDS team are the heart of what you do, and the results are constantly showcased in the form of success stories and case studies at conferences around the world. Why are they such a draw for customers?
Today we have about 500 success stories: articles at symposium/conferences, external/internal MDS stories. I track all of them and every year we present several papers at global conferences such as Turbo in Houston, EFRC, Asia Turbo, ADIPEC and also regional conferences.
If someone wants to become a part of your team, what should they do to prepare themselves for this career move?
We welcome any engineers. My vision is that any engineer can be part of MDS. There is no need to be a vibration specialist before joining MDS as we have all the trainings and people to teach what is needed. In my opinion, the most important thing is the mindset, the wish to learn, and the taste for machines…being an MDS is more than a job. MDS is also a school and we want to see our engineers grow technically and know that MDS offers a technical career path!
What is unique about Bently Nevada MDS?
TheMDSteam is not just a collective group of experienced and driven field engineers but it we also aspire to be a community of like-minded engineers motivated to better understand the machinery in their care and solve the problems that might stop them from doing that. The MDS team attempts to provide an environment where anyone in the team is encouraged to both contribute to and learn from the wider team. We also take pride in trying to develop our own people; meaning if they wish to progress into a Technical Leader or even Director that option is open to them if they are willing to do the work.
What type of tools do you need to do your job?
An inquiring mind and a disposition to be a problem solver are a good start but in terms of actual tooling, almost any form of data collection device could be of use. These could include tools often associated with MDS, like the ADRE or SCOUT, and of course, System 1, however, at a higher level you could say any data or information that we can track over time to inform us of a machines condition is our main tool.
Please share with us the direction and future of the BN MDS organization through the lens of a leader.
Over the past few years, we created the position ofCondition MonitoringTech Lead to expand our knowledge around process and auxiliaries. We have also introduced/developed several new tools such as structural vibration, torsional analysis, motor current analysis, optical ODS, more analytics and better monitoring views…
My vision is to merge MDS and Condition Monitoring engineering, as in fact MDS stands for Machinery DiagnosticsServices and not VibrationDiagnostics Services. An MDS engineer must be able to deal with vibration data, process/performance data, auxiliaries data (oil, water, gas, steam, etc.), control system, analytics, and more.
Today, there is a trend that is claiming that the self-learning systems with neural networks and pattern recognition can get to conclusions straight from the data by automating the information digging and processing, without external knowledge. However, these systems cannot achieve that. They need knowledge and meta knowledge for creating education patterns, models and for monitoring if the output results make sense (validation). So, in fact there is no conflict because there are no pure self-learning systems or pattern recognition systems. You still need experts and procedural modules (math models and rules).
The worse and, from my perspective, unacceptable scenario is when someone is promising “a magic solution” that is providing answers without pyramid structure. That is promising more information than your data contains. For instance, you are promising that from current signature, you can diagnose the misalignment between the machines or, from single probe, you can diagnose “all problems”. Clearly, this is fantasy notMachinery Diagnostics.
MDS is helping to develop first principal rules using our 60 years of experience and is also helping to develop solution-based AI models. In the end, it is not who has the best algorithm that wins, it is who has the best and most relevant data. So, customers have challenges and we (Bently Nevada) have solutions that interact within boundaries. Our story is: we measure and protect the machines (our hardware), we display ALL of the data, we diagnose and notify automatically using our methodology and 60 years of experience, we can export our data (modbus, OPC, etc.) and we have THE relevant data (we have the raw data but we also have extractions (so engineering features)) and results/events) to be used with AI tools. MDS is involved with all of that. AI will be helping us triage our workload and work more efficiently but it will not be replacing MDS any time soon.
During Covid 2020, how has the MDS team pivoted to support our employees and customers? How will they continue to support through the pandemic into 2021-2022?
In 2020, MDS supported around 300 remote jobs (remote trainings, remote reactive MDS jobs using S1, ADRE, etc.) with an impact of about $3,000,000 USD.
People should remember that this is not something new. Already in the 1990s MDS was supporting our customer remotely, MDS was already moving the data and not the people.
Our Technical leaders did a great job of adapting our courses to teach them remotely, they pushed our MDS to use remote solutions to support our customers. All of this is not new, Bently Nevada has always been innovative.
What type of feedback is the MDS team receiving from the BN employees and the customers during the 2020 year that we can grow from and continue to support them with, with the lack of interaction while previously being face to face?
远程工作,虽然不是新MDS团队,has seen an increase in 2020-2021, allowing us to faster refine and improve on what we were already doing with more training material and customer-facing solutions created to allow our team to be more effective, even remotely.
What does MDS mean to you, to our employees, and to our customers? Why is it so important?
To me MDS is my heart, this is my dream job! I do not think there is a more interesting job than being an MDS. For the MDS team, I hope it allows them an opportunity to relish in the technical challenges and the ‘detective story’ each new case might bring. For our customers, we might be the last chance they have at understanding the issue - as we are often called when local diagnostic efforts are exhausted, so we are the trusted experts. In the long term, maintaining that trust with our customers and upholding our reputation as the team of trusted experts not only allows us to deliver significant review for the business but also critical real-life experience for our engineering and product teams. This will help keep BN software and hardware at the leading edge of the market.
Nicolas Peton
MDS Director
Bently Nevada, a Baker Hughes Company
Pamela Litka
Marketing Operations Specialist
Bently Nevada, a Baker Hughes Company
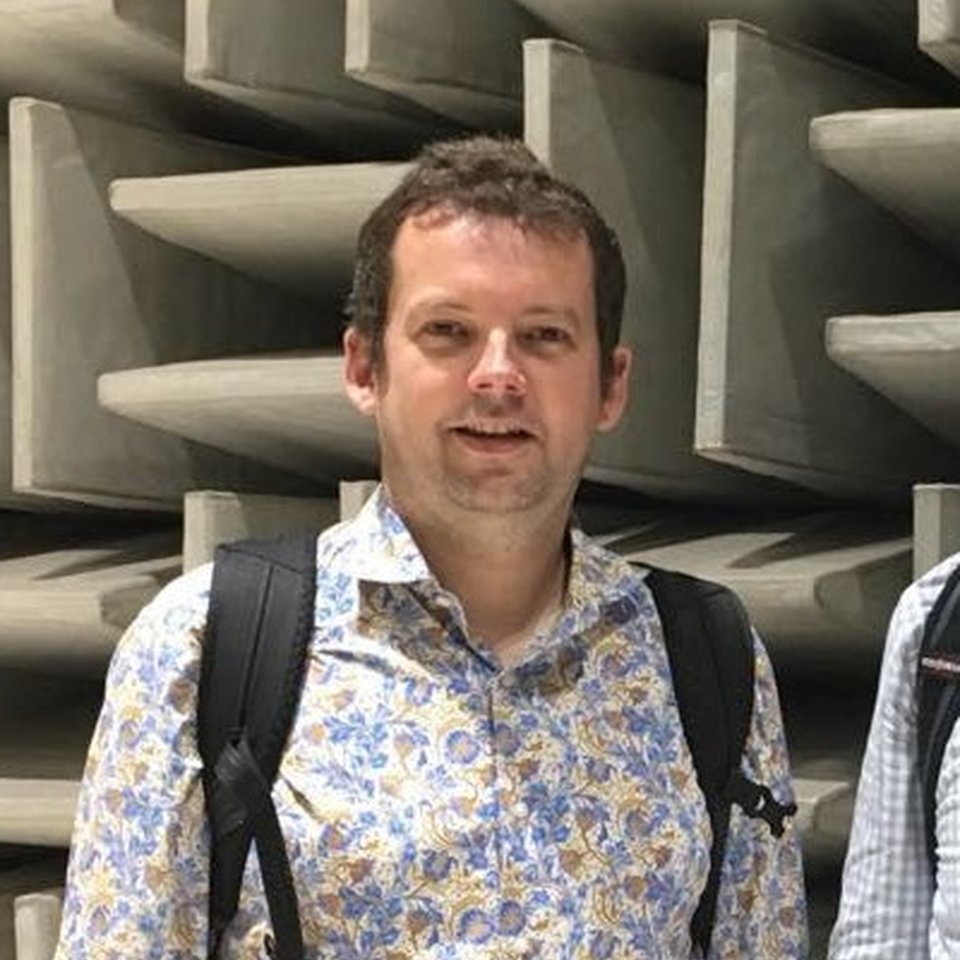
Nicolas Péton, PhD
MDS Director
BIO
He is currently MDS Global Director for the Machinery Diagnostic Services.He joined Bently Nevada in 2006 and has always worked within the MDS team. He has more than 25 years of experience.