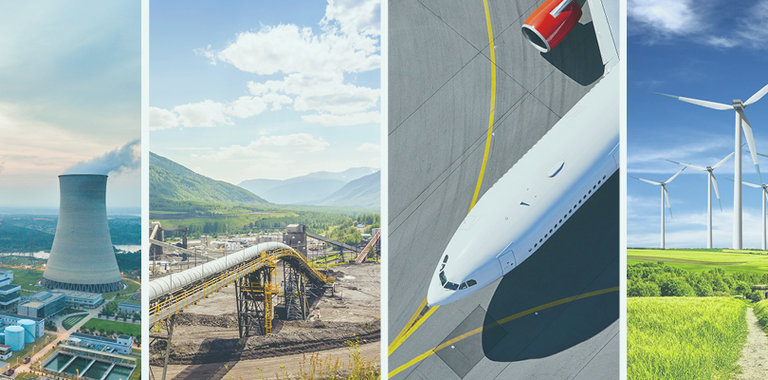
Proximity probe system interchangeability, don't build a "Frankenstein" system!
Proximitor® probe systems based onEddy current technologyhave become common place in industrial plants these days. Everywhere a medium or high criticality machine is running, chances are that non-contacting eddy current systems are installed and are used for condition monitoring measurements and/or automatic machine trip or shutdown. More often than not, Bently Nevada Proximitor® probe system is used to protect and monitor these machines.
From the very first days that Don Bently invented and pioneered the use of the eddy current Proximitor® probe in the late 1960’s, quality, reliability and ease of use have been among the top priorities at Bently Nevada.
That tradition, rooted in our passion for customer service, is still alive and well today. And it is no more apparent than it is with our commitment to full interchangeability with our Proximity probe systems.
With respect to Proximity probe systems, interchangeability refers to the ability to interchange the probes, cables, and Proximitor® sensors easily without the need for calibration or special tools.
For example, the most popular line of Bently Nevada proximity probe systems is the 3300XL 8mm system. Interchangeability means that with this system a plant can easily exchange 3300XL 8mm probes, cables, and Proximitors® without any significant change in output such as gap voltage or direct vibration.
Interchangeability is an important advantage. In the early days of eddy current system development, each probe, cable, and Proximitor® had to be tuned to match one another in a unique set. Anytime that a piece of the system needed to be replaced, a spare for that system that was an actual calibrated match was required. This meant that each vibration point on a machine potentially needed to have its own spare. On a typical 4-bearing machine this might mean the plant would need to stock or calibrate many different spares, in some cases, one for each eddy current driver, cable, and probe.
这是一个非常昂贵,复杂,耗费时间, endeavor. Bently Nevada answered the need for a better way and pioneered the development of our gold standard technology that ensures complete interchangeability between the main Proximitor product families. As shown above, each family of Bently Nevada Proximitor has its own color-coding for easy identification.
Bently Nevada uses a metrology tracked gold standard system to ensure that a 3300XL probe purchased 18 years ago works correctly with a 3300XL Proximitor module you buy today and an extension cable you may buy 10 years from now. No one else in the industry besides Bently Nevada can claim this level of rock-solid performance AND interchangeability.
A simple example that plays itself out regularly at plants around the world regardless of industry is one in which either a cable or Proximitor needs to be replaced. It could be that an electrician accidentally stepped on a piece of conduit severing the probe cable. Or perhaps a Proximitor was damaged during installation or wiring or even a steam leak that “cooked” the sensor. Whatever the cause, no matter how bullet-proof the design of the Proximitor, it is a precision instrument and plants do need to replace them from time to time.
Without interchangeability, unless the plant actually stocked the exact calibrated match for the Proximitor or probe cable that was severed, there is essentially no way to replace the part and ensure that the reading is correct. The plant would need to shut down the machine, remove the machine covers, and access the bearings to be able to replace all three at once: probe, Proximitor, and cable, to ensure the reading is correct. In some industries that may not be an issue. In the critical process industries where equipment is expected to run for years without stopping, it is unacceptable.
With a fully interchangeable system like the Bently Nevada 3300XL, the plant simply replaces the damaged Proximitor or cable with an off-the-shelf spare part and continues to run, no calibration or special tools required and no need to disturb the probes installed deep within the machine. In fact, because of our gold standard and unmatched interchangeability, all of the machines at the plant can use exactly the same Proximitor drivers and cables and with a few different probe options, the plant’s entire needs can be covered by just a handful of spare parts shared amongst all the machines, which lowers maintenance costs and reduces the chances of system mismatch.
A typical Bently Nevada Proximitor, probe, and cable set is engineered to work together as a system. The discussion above gave us some background on what interchangeability is and why it is important to your operation. If you take the discussion a bit further and examine the mixing and matching of eddy current system parts from different manufacturers, you encounter the so-called “Frankenstein” system.
A Frankenstein system mixes and matches parts from different manufacturers that were never designed to work together. Whether out of a perceived cost savings, a simple lack of experience, or other factors, several plants have incorporated parts from different manufacturers to create these mixed-and-matched systems. At first, during installation they may appear to work correctly. However, several customers have experienced serious problems as a result of using the Frankenstein approach.
Case in point: One of our key customers operating a refinery in the Middle East recently called their local Bently Nevada Field Service office and complained that production was down because of intermittent machinery shutdowns of some of their critical turbomachinery. The Bently Nevada system was suspected of causing false trips and the customer was quite upset. Within hours a local Bently Nevada Field engineer from that region was on site to diagnose the problem.
Upon investigation it was discovered that all of the Bently Nevada Proximitors had been removed and replaced with something else. The Bently Nevada probes and cables were still in place but the Proximitor that was compatible with them using the Bently Nevada gold standard at the factory had been replaced with a competitor’s eddy current driver in the field with unknown electrical characteristics.
Upon discovering this, the refinery management launched an internal Root Cause Analysis (RCA) and determined that the mismatched eddy current driver was the source of the false trips. By changing from a Bently Nevada Gold Standard Proximitor with known characteristics and replacing it with a competitor’s unknown product, the plant inadvertently “changed” critical machinery set points without knowledge of the plant operations group! How were the setpoints effectively changed? Examine the results of the mixed system that was tested in the plots above. Clearly it can be seen with both the 5-meter system (left side plots) and the 9-meter system (right side plots), that the non-linear response and error of the mixed system can essentially “change” intended setpoints.
The shocking level of difference in the performance of the Bently Nevada system vs. the competitor’s product, and especially the difference in the mixed Eddy current system, is explained by the difficulty in manufacturing accurate, reliable Eddy current systems. These systems are relatively easy to manufacture and market, they are however very difficult to manufacture with repeatability and accuracy. This is what Bently Nevada has done so well for the last 50+ years and what separates us from our competition.
In addition to that, no manufacturer will warranty the mixing and matching of transducers and the consequences of that choice are completely in the hands of the end user and in some cases could lead not only to loss of production at the plant, but also unsafe conditions and risk to life and limb.
Since its release in 1999, Bently Nevada has manufactured approximately 2 Million+ 3300XL systems with 100% testing on each and every system. We have full access to the statistical process control data and are constantly fine tuning to ensure every part is as consistent as possible. We even have data based on serial number going back decades that we can refer to for RCA purposes, a level of expertise it is very difficult, if not impossible to find with other manufacturers.No one else takes this to the level that Bently Nevada does.
So how can setpoints be effectively changed without the knowledge of your machinery team? Take for example the process that the plant went through to determine the correct alarm set points for the machine. The following hypothetical sequence of events is only representative but gives you a sense of the time, effort, and expense that a plant will incur to determine and implement correct set points and appropriate relay logic for a typical critical turbomachine, and how the whole process can be inadvertently circumvented.
- The plant orders a pair of motor-gearbox-compressors for a new expansion at the refinery.
- The OEM delivers the compressors along with recommended alarm setpoints for vibration and thrust.
- Three OEMs are involved: motor, gearbox, compressor.
- All three OEMs have different recommended setpoints.
- Plant reliability and consulting engineers have their own desired setpoints different from the OEMs.
- Many meetings between the plant staff and OEM engineers ensue and eventually agreement is reached on the initial alarm setpoints.
- Installation project completed.
- Commissioning completed.
- Successful machine startup, and production begins.
- The operation of the machine has now been handed over to operations.For any changes to be made to the system at this point, an extensive Management of Change Process or MCN must now be followed-and for good reason: the amount of work that went into determining good setpoints and relay logic, and the risk of lost production or damage to the equipment if an error is made cannot be over-stated.
- If we fast-forward one year into operation, the plant reliability engineers wish to make a change to one of the thrust setpoints based on a catastrophic failure of the same machine at another plant.
- The full MCN process is then followed which includes many meetings outlining the reasons for the change. In the end in this case, the plant manager has to sign the MCN to allow the change to take effect.
Let us reiterate that thePlant Managerin this case had to sign the MCN for a simple setpoint change that was very well documented and justified.
The point in documenting this process is to show that if a Proximitor on these machines is replaced, either because the Proximitor was damaged, incorrectly installed, or part of a routine maintenance, with a non-Bently Nevada driver and the Bently Nevada probes and cables are left in place, that this becomes a mixed-system or so-called “Frankenstein” system. The whole process outlined above, trusted by the Reliability Engineers, operations, the OEMs, the plant manager, and even the shareholders, used to ensure the safety, reliability, and financial viability of the operation has been inadvertently circumvented and bypassed. And it was all done because a 2nd vendor stated: “Our Eddy current driver is compatible with Bently Nevada probes and cables.”
Even more concerning is that it happened without a substantive process, evaluation, or the knowledge of many of the key stakeholders above. Because the gap voltage of the mixed-system still reads essentially the same during installation (see Gap Voltage plots above), the plant in many cases has no realization that all their setpoints have effectively been changed without process!
As mentioned earlier, some competitors have claimed that their eddy current drivers are compatible with Bently Nevada probes and cables, even to the point of using our own part numbers, this is breeding misinformation. The system will appear to work at first but according to our testing will often give erroneous readings. While the machine is not running during installation the gap voltage can show similar levels, it can be seen clearly in the plots below what happens to the vibration measurements with a mixed system when the machine is running. Across the range of gaps in the sample testing that was done, the vibration in the 9-meter system (shown above) is generally attenuated-especially above 50 mils of gap as can be seen in the center plot of incremental scale factor (ISF). At the extreme gaps the displayed vibration for the mixed-system can be attenuated by as much as 25% or more. The ISF actually disappears above 80 mils of gap dropping below 150 mV/mil on a system that is supposed to be 200 mV/mil! The 5-meter system that was tested actually shows the opposite in this case with greatly exaggerated vibration. Without the use of the Bently Nevada Gold Standard, the competitor’s transducer system has little chance of being within specification. Depending on each probe and Eddy current driver, the levels could read high or low.
The consequences of the attenuation are more than inconvenient. If the current vibration reading with a 9-meter system at a given point on the machine is 6 mil P-P using a competitor’s eddy current driver, the actual vibration could be in excess of 8 mil PP or more! This could mean the difference between continued smooth operation and a costly unplanned outage or even a machine crash.
More concerning than even this is the impact an erroneous reading has on a critical thrust protection measurement. Devastating thrust failures can happen within milliseconds, long before a human being has the ability to react. Because of this, many systems use dual voting or even a Triple Modular Redundant (TMR) thrust system. The implications of the incorrect scaling of a Frankenstein system in this scenario are even worse.
Bently Nevadahas the following recommendations to keep your operation reliable and safe.
- Avoid the “Frankenstein” system.Never mix eddy current (Proximitor) systems using parts from different manufacturers. If you decide to use one of our competitor’s systems, make sure you are at least using eddy current parts (probe, eddy current driver, and cable) from a single manufacturer-even if it is not Bently Nevada. Using mixed systems will also likely violate any system certifications.
- Always use a genuine Bently Nevada Proximitor® product.Use only genuine Bently Nevada Proximitor, probes, and cables, our Proximitor systems are based on a proprietary gold standard available to no one else and have the highest reliability and guaranteed performance over a very wide temperature range. Bently Nevada also holds a suite of certifications including hazardous area, intrinsically safe systems, and country specific approvals that none of our competitors can match.
- Evaluate the Performance.Regardless of what Proximitor or eddy current system is used, fully understand the reliability, and accuracy of the system, especially over temperature. Refer to industry standards and specifications such as API 670. Even if your industry is not the Petroleum industry, this specification is quite often used as a general guideline in all industries operating critical rotating turbomachinery and reciprocating machinery.
- Keep the Whole “System” Reliable.Bently Nevada 3300XL Proximitors探测器和电缆,使用时在一起,形成一个engineered transducer system that is extremely reliable. In addition, consider that the selection of the system monitor or protection system is equally important. The Bently Nevada 3500 Machinery Protection System incorporates all of Bently Nevada’s 50+ years of machinery knowledge. That knowledge has been learned the hard way through many experiences similar to the one outlined above, knowledge that we fed back into our products, that gave us the outstanding reputation that we have today. In short, Bently Nevada is exceptional at data acquisition and also at detecting and preventing two key things: missed trips and false trips. For critical machinery we are the best in the world at this.
除了一些陷阱earli概述er, some companies provide the ability to adjust the limits and outputs of the eddy current system. Some, touting the ability tune the output to “API standards”. In the early days of eddy current technology this was an accepted method (used also by Bently Nevada in those days) to produce an accurate system. As technology progressed and the use of the gold standard was implemented, it was no longer required for a customer to “tune” the eddy current driver. Some companies still rely on this legacy approach, even advertising it as an advantage, because they do not have the ability to produce the world-class gold standard technology that Bently Nevada has.
In addition to this, having produced and installed an estimated 4 MillionProximitor systemson the world’s most critical equipment, our experience shows that customers do not benefit from an “adjustable” system.
首先,可以校准传感器通常required to be recalibrated on a scheduled basis. The issue with this is that there are no calibratable degradation modes in any eddy current sensors, regardless of the manufacturer. If the sensor scale factor drops, the affected component needs to be replaced, not recalibrated. Under no circumstances should aneddy current sensorinstalled in a machine be recalibrated due to degradation, as this can lead to significant measurement error over time, essentially “tuning out” the degradation and blinding the plant to high vibrations or extreme thrust position.
Another problem relates to troubleshooting and stems from the fact that once the system has been installed and adjusted, the question always arises whether or not it was adjusted correctly? Did the technician set the correct upper and lower limits? Did they get adjusted at some later date? This uncertainty becomes a real issue when a machine begins having a vibration problem. The first question that is asked is whether or not the instrumentation was “adjusted” correctly. Instead of focusing on the vibration issue, the customer is focused on diagnosing and/or validating the transducer system! When a Bently Nevada Proximitor system is used, it requires no adjustment, therefore, this uncertainty is removed and the measurement can be trusted for shutdown or diagnostics.
Not only do we calibrate our 3300XL Proximity probe systems to our proprietary gold standard as mentioned above, we do this calibration in an automated manner using robotics on fully NIST traceable equipment. We have done this 2 Million+ times with 3300XL…and counting.
现实世界广泛提供的机器of shaft materials. Since the non-contacting eddy current system is sensitive to the particular alloy of the shaft, the eddy current sensor needs to be able to handle these various materials and provide a consistent, accurate output. Again, some companies claim the ability to “adjust” the output of the eddy current system to any shaft material as an advantage. Unfortunately, they end up in the same situation as outlined above with a system that is adjustable but may or may not have been adjusted correctly, leading again to uncertainty or a system that has had the degradation “adjusted-into it”. Bently Nevada offers a complete library of Proximitors for common (and uncommon) materials, each with their own genuine Bently Nevada gold standard so that customers do not have to worry about “tuning” their system in the field.
Bently Nevada takes the reliability and safety of our customer’s operations very seriously and over the years we have labored to earn your trust with your most critical machines. In turn, you have come to trust in our solutions and our expertise and the fact that we do not compromise when it comes to safety, quality, and reliability. This is our commitment to our customers now and into the future.
Our Experts
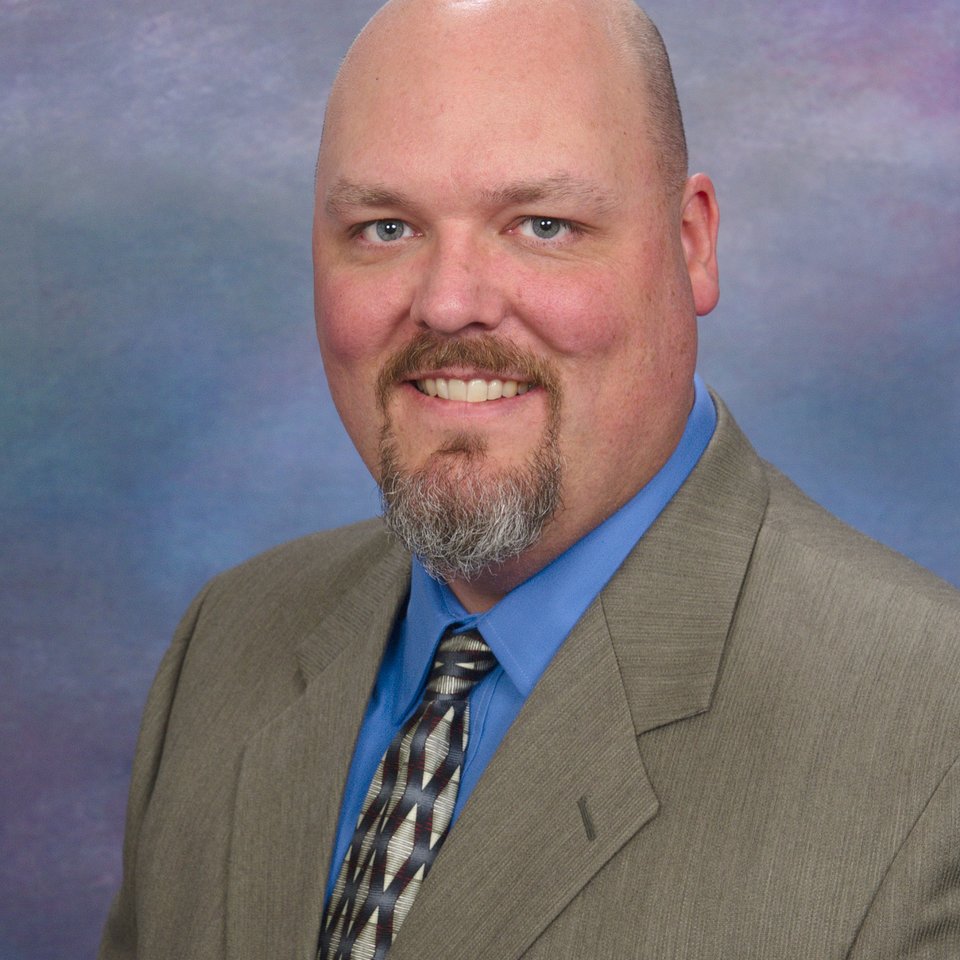
Brant Wilhelm
Global Technical Support Manager
BIO
Brant Wilhelm has been a part of the Bently Nevada family for 15 years and has held leadership roles in Services, 3500 Product Line, Transducers, and Remote Monitoring.