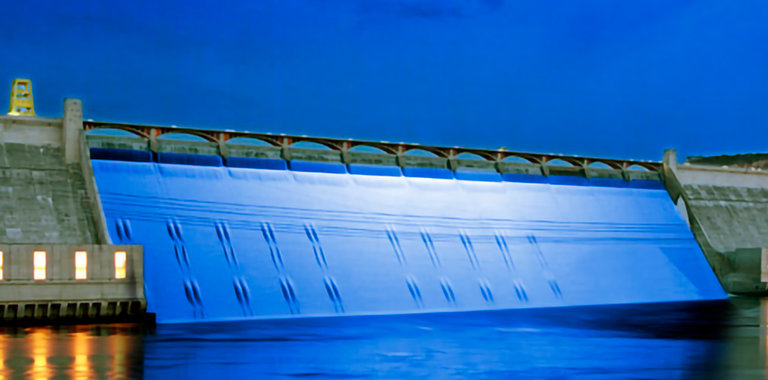
Smart monitoring for the intelligent machine age
Older machinery protection systems, and even transmitters (Reference 1) and simple vibration switches marketed today, only produce a “Direct” (broadband) vibration measurement. Since the Direct value contains contributions from all sources of measured vibration, it is the one measurement that can provide a comprehensive representation of the overall health of the machine. However, relying on this measurement alone has drawbacks.
One problem is that because the Direct measurement is typically used to alert operators or trip the machine, Direct alarm thresholds are set relatively high to suit all situations and prevent false alarms and trips. Consequently, these alarms and trips ignore notable vibration changes in all but the worst-case operating condition.
Another limitation is that Direct vibration alone merely provides an indication that there is (or has been) a problem, but provides little or no useful information to help you answer the next logical questions of what is causing the problem, and what operational or maintenance actions should be taken to mitigate or correct it.
This article describes how an effective machinery protection/ condition monitoring system solves these problems, and how the 3500/46M Hydro Monitor addresses the unique needs of hydro turbine generating units.
Today’s microprocessor-based machinery monitoring systems can perform signal processing functions that once required bulky portable analyzers. This enables the monitor to break out several components and characteristics of the broadband vibration that can serve as useful diagnostic “clues.” A good analogy is a musical chord. An untrained ear can only tell that the overall sound is dissonant, but cannot tell which of the notes is out of tune. However, if each note that makes up the chord is played individually, even an untrained ear can usually pick out which note is causing the dissonance. Similarly, exposing individual values that make up the broadband vibration can help classify the type of machine problem.
解锁这些个人价值的关键incorporate a once-per-turn phase reference measurement made by a Keyphasor* monitor. Previous Orbit articles have defined and described the concepts of phase angle and the Keyphasor measurement (References 2 & 3), and the following is a summary of the functionality and benefits that a Keyphasor measurement provides.
- A Keyphasor transducer is necessary for in-place machine balancing; anyone doing balancing needs the once-per- turn reference that the Keyphasor channel provides.
- A Keyphasor signal enables the calculation of “synchronous” data – data that is taken by synchronizing the vibration waveform sampling rate with the running speed of the machine. This preserves the accuracy of phase angle measurements and the amplitudes of vibration components that track with machine speed.
- A Keyphasor signal allows the monitoring system to filter around (isolate) only the vibrations that have the same frequency as running speed or multiples of running speed (1X, 2X, etc.) - even during machine speed changes.
- A Keyphasor measurement provides a phase angle value associated with the filtered amplitudes of each transducer measurement. Phase can be just as useful as amplitude for detecting changes in the machine behavior. In fact, phase angle may change even when there is no increase (or even a decrease) in vibration amplitude.
- Portable analyzers and data acquisition equipment need a Keyphasor signal to generate the values and graphical plots necessary to definitively identify a machinery problem.
The value of filtered amplitude and phase angle values (e.g., vector values) for machinery monitoring and predictive maintenance is widely recognized. This concept is acknowledged in a well- known international standard on hydroturbine vibration monitoring (Reference 4). Main points are summarized here:
- Broadband vibration amplitude (without frequency or phase information) is usually adequate for operational monitoring and acceptance testing.
- However, vibration vector information is especially useful for machinery diagnostics and long-term condition monitoring.
- Some changes in the dynamic state of the machine cannot be detected and identified by broad-band measurements alone.
With a Keyphasor signal available in the 3500 monitoring system, the 3500/46M (and other 3500 vibration monitors) provides a number of useful variables in addition to overall vibration (Figure 1). Guide bearing (shaft relative) vibration, casing absolute (acceleration, velocity) vibration, and generator air gap channel types will have different variables as appropriate to their intended applications. All of the variables’ values can be viewed and compared in real time on a local display, and sent via Modbus to a SCADA or control system for trending.
Changes in these values can provide clues to the cause or characteristics of a machine problem.
Generally, changes in 1X Amplitude and Phase are related to imbalance and misalignment. Phase angle is useful for detecting shifts in the inertial, hydraulic or magnetic forces acting laterally on the shaft or runner, such as from loss of material from one side of a runner, blockage of one bucket of a runner, a deviation from the normal flow through a needle valve, and other problems.
Changes in Not 1X vibration are typically symptoms of rubs, fluid-induced forces in the bearings or at the runner, or rough load zone and vortexing. The “N” value in NX Amplitude can be set to “2” to indicate rotor cracks and other changes in stiffness, or to the number of runner buckets to detect hydraulic imbalances associated with wicket gates or nozzles.
3500/46M还提供了平均距离公关obe gap measurement for radial vibration measurements. This can be used to monitor shaft journal position within the guide bearing, which could change due to misalignment and preloads. Gap alarms can be set to indicate when the normal bearing clearances have been reached or exceeded (corresponding to potential or actual bearing wear). Also, this gap measurement, in combination with the NX measurement set to the number of runner buckets, is used in the 3500/46M Hydro monitor to calculate a “Composite” value that can indirectly detect a shear pin failure in the wicket gate positioning linkage.
Now that we have several values to give a more complete picture of machine condition, the other challenge is to set alarm levels that are appropriate for different machine operating conditions. Using another musical analogy, most compositions contain both loud and soft segments, and the softer passages usually cause the audience to quiet down and listen more carefully to hear the subtle melodies. Similarly, a good monitoring system should adjust its alarms to “listen” more or less closely when varying conditions change the “acceptable” vibration levels for long periods of normal operation or for short periods during a start-up sequence and other operational transitions.
One relatively simple way of dealing with the transient conditions is to use the Trip Multiply feature found in the 3500/46M and other 3500 vibration monitors. Trip Multiply temporarily elevates alarm levels by a factor set for each channel in the configuration software (see Figure 1). Note that the Not 1X alarms can be excluded from the Trip Multiply activity for that channel, which might be desirable if vibration excursions other than 1X are of concern during the transitory conditions. The Trip Multiply condition is actuated for all monitors in a 3500 rack using a pair of contacts on the 3500/22 TDI Rack Interface I/O module, or for groups of monitors using a Modbus digital input via the 3500/92 Communications Gateway.
抽水蓄能机组rotati两个方向on with vastly different hydraulic conditions. Kaplan units with adjustable blade angles can have significantly different levels of “normal” vibration, and any hydro turbine usually has at least one zone of high vibration associated with certain unavoidable head, speed, and load conditions. To accommodate these situations, the 3500/46M has a “Multimode” feature that allows you to establish up to eight (8) distinct machine modes, each with its own unique set of alarm parameters.
The user-defined modes are enabled and named in the 3500 configuration software (Figure 2). Typical modes would accommodate operating conditions such as forward rotation, reverse rotation, loaded, unloaded, high head, low head, etc.
Once the modes have been defined, you can select each mode and set the alarm parameters for the variables of each channel as appropriate for that mode. You can enable or disable the setpoints, define the setpoint levels, and adjust the alarm time delays as needed (Figure 3).
The multimode channels of a monitor must be “told” what operating mode the machine is in, so that they can use the correct alarm settings for each mode. Mode change commands from the control system or other source can be input via wiring terminals on the 3500/46M Multimode I/O modules, or digitally via a Modbus write command feature of the 3500/92 Communications Gateway Module.
In the age of smartphones that incorporate music players, cameras, portable digital assistants and mobile GPS devices, it no longer makes sense to use a “dumb” monitoring system to make intelligent machinery protection and condition monitoring decisions. Microprocessor technology has made it possible to embed powerful signal processing capabilities - once available only in bulky and cumbersome portable analyzers - into every channel of an online machinery monitoring system, while enhancing the effectiveness of these systems for reliable machinery protection.
This enables the monitor to produce a steady stream of diagnostic-quality data both locally and remotely, in real time and for trending in plant historians as part of a predictive maintenance program. The features of the 3500/46M Hydro Monitor can extend your monitoring system from a device that simply tells you when to shut a machine down, to a powerful predictive maintenance tool that helps you keep your hydro turbine generating units humming smoothly.
In a future Hydro Corner article we will describe how the Multimode feature of the 3500/46M monitor can work hand-in-hand with the State-Based Analysis features of System 1* analytic software to enhance and simplify trending and diagnostics across the varying operating states of a machine.
- Orbit Vol.18 No.1, 1997. Sabin, Steve, “The limitations of protecting and managing machinery using vibration ‘transmitters.’”
- Orbit Vol.20 No.2, 1999. Forland, Clair, “Why phase information is important for diagnosing machinery problems.”
- Orbit Vol.32 No.4, 2012. “Designing and Machining a Keyphasor Trigger”
- ISO 10816-5, 2000. International Organization for Standardization, “Mechanical vibration — Evaluation of machine vibration by measurements on non-rotating parts - Part 5: Machine sets in hydraulic power generating and pumping plants”, Paragraph 5.7.