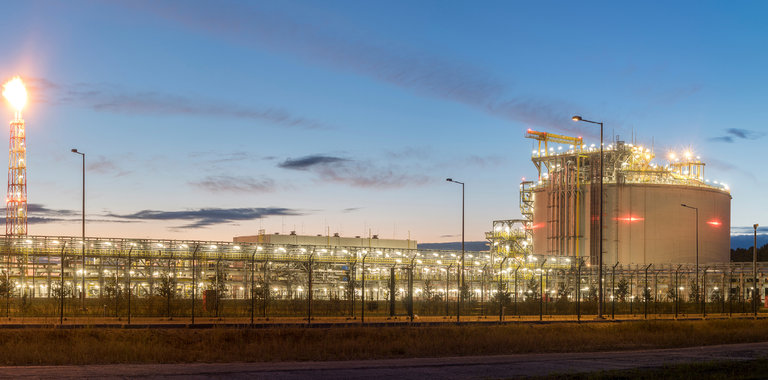
Trendmaster and its new Software
But before we show you the details aboutthat, let’s take a step back and reviewwhat is aTrendmaster monitoring system, and where does it fit into your plant’s asset reliability program?
(If you’re already proficient with Trendmaster, then feel free to jump ahead to the Condition Monitoring Software section)
Different machines require different strategies & technology – not all machines are created equal. Some assets, such as large un-spared process compressors, have the entire plant process flowing through them, so represent an enormous lost production risk if they don’t run. Others, such as the hundreds of small pumps, motors, blowers, fans, fixed equipment and other assets that populate a typical plant, are spared or may have a minor impact on plant output when they fail. But they represent appreciable collective maintenance costs and can benefit from some form ofcondition monitoring. Still there are other assets that simply don’t merit much more than a “tighten the bolts, change the oil” approach without any routine condition monitoring. And finally, there is a class of assets that falls somewhere in the middle — benefiting fromonline monitoring, requiring more than intermittent gathered data, but not able to justify the expense of protection-oriented fully online monitoring systems such as3500orOrbit 60.
Table 1 summarizes the four broad asset categories most frequently used by customers when considering the type of condition monitoring to apply.
See full details:
- Tier 1 - Continuous online monitors (e.g.3500,适应,Orbit 60)
- Tier 2 - Continuous or scanning monitors (e.g.Trendmaster®,vbOnline Pro, orRanger Pro)
- Tier 3 - Manual data collection (e.g.SCOUT series portable instruments)
* A relatively small number of Tier 2 assets may benefit from basicmachinery protection. Bently Nevada offers 1900 & 2300 series monitors for use in such circumstances. These small, stand-alone devices provide basic continuous machinery protection capabilities and are appropriate for machines where only a few measurement points can adequately protection the asset. 2300 series monitors include an option for direct interface to a Trendmaster® system.
而这些categorie的名称和定义s are sure to vary between customers and global regions, the concept of combining risk likelihood and consequence into a tiered classification like this is almost universal.
Historically, equipment in both Tiers 2 & 3 was monitored by a manual data collection program utilizing portable振动测试和分析工具to take periodic readings. However, the machines in Tier 2 have been an increasing source of concern to plant manager, who are not always able to meet their objectives using a manual data collection strategy. They have expressed needs such as:
“Failure on these equipment assets seems to be related to process conditions, but by gathering data only once a month or so, it is impossible to establish any kind of meaningful correlation or cause/effect understanding. I may be able to identify the parts that are failing but can't get to root cause to stop them from failing again.”
“I catch some failures, but others spring up faster than my data collection interval can cover, and I can't afford to collect data more frequently by hand.”
“I’d like to collect data, but the places I need to make measurements on these equipment assets are too hazardous or inaccessible.”
“The facility is remote and/or un-staffed. It is too expensive to send someone in just to manually collect data.”
“These assets don’t warrant the same type of system as my critical assets, but I don’t feel like I have any alternative if I want online monitoring.”
“I take portable readings, but I’m not happy with the variation I get with hand-held transducers from one day to the next. I think permanently mounted transducers would provide better results.”
“My labor costs are rising, and my staff is shrinking. I need to automate portions of my condition monitoring program because I can't afford to use people solely to collect data — I need them to focus on fixing identified problems and improving reliability.”
“I want to address more than just rotating machinery with my condition monitoring program — I have to maintain fixed equipment in my plant that includes electrical as well as process equipment. I would like a system that could cost effectively bring all my machinery and fixed equipment asset information together into a common tool.”
These types of industry needs prompted Bently Nevada to develop the Trendmaster® 2000 system back in 1989. The Trendmaster system is founded on these simple ideas:
- Permanently mount low-cost transducers on the equipment.
- String these transducers together using a special network, allowing multiple transducers to share the same multi-drop cabling.
- Instead of an individual monitor channel dedicated to each transducer, one channel multiplexes (switches) across many transducers, polling each transducer one at a time.
- Optimize the cost for intrinsically safe operation of the transducers and cabling, allowing economical use in hazardous areas.
This figure demonstrates how Trendmaster compares with a traditional rack-mounted monitoring system:
Clearly, Trendmaster represents a less expensive solution for permanent monitoring, by using its innovative sensor bus and scanning architecture. Some might be tempted to use Trendmaster for high-speed, critical, multi-case machine trains (Tier 1). However, the failure mechanisms of these machines can occur rapidly and require a system that is protecting the machine with every shaft revolution. Furthermore, diagnostics on Tier 1 machines are often more complex than those of smaller “essential” machines with only a few bearings and simpler rotor dynamics. For these reason, Bently Nevada continues to advocate, and customers continue to prefer, our continuous machinery protection systems for Tier 1 assets.
Trendmaster could be applied to theleast criticalclasses of assets (Tier 3-4), however this would generally not be justifiable economically.
So, essential (Tier 2) really is the target for Trendmaster applications. These include cooling tower fans, heat exchanger fin fans, blowers, fixed equipment, and others. In petrochemical industries a key application is pumps which not only have bearings and seals that can fail relatively rapidly, but also risk the release of hydrocarbons and hence the possibility of fires. We have also seen widespread deployment of Trendmaster systems in the cement industry, pulp & paper, steel, pharmaceuticals, mining, power generation for “balance of plant” assets - and numerous other applications where online health monitoring of important assets is warranted.
Those of you who are familiar with Bently Nevada’s range of condition monitoring products will know that it does contain others which are also suited to tier 2 assets. For example, the 12 channel vbOnline Pro, and the Ranger Pro wireless system. These are both excellent solutions, and fully supported by System 1. However, each application has its own unique requirements, and Trendmaster brings these key advantages:
Compared to vbOnline Pro:
- Trendmaster is more suited for installation in hazardous areas
- Trendmaster supports more than just accelerometer and speed measurements
Compared to Ranger Pro wireless:
- Trendmaster can take measurements more frequently
- Trendmaster has no need for periodic battery replacement
- Trendmaster supports more than just accelerometer and temperature measurements
Trendmaster consists of five main components, and we consider each of these in the following sections:
- Transducers
- Transducer Interface Modules (TIMs)
- Cabling and Accessories
- Dynamic Scanning Modules
- Condition Monitoring Software
Transducers are permanently mounted on the assets and take the fundamental condition measurements. A wide variety of transducers and input signal types are supported by the Trendmaster system, as shown in the following table. These include vibration & speed sensors, and other process parameters like temperature and pressure.
Trendmaster can accept vibration measurements from a very wide range of vibration transducers, however the most cost-effective approach is to use transducers developed specifically for the Trendmaster system. These address the simultaneous requirements of low cost, rapid and inexpensive mounting, hazardous area certification, electrical compatibility, robust environmental design, and performance characteristics that meet or exceed the diagnostic requirements of most Tier 2 assets.
See full details:
TIMs provide power to the transducers and some signal processing to prepare the signal for transmission on the sensor bus cable (i.e. TIM Line). The TIMs assign a unique address to each transducer or signal input location.
Over the years, TIMs have taken on several different physical form factors, as shown in the following table. The latest ProTIMs are easy to install, easy to configure, provide better self-diagnostic capabilities, and you can mix and match channel types.
TIM cable forms the backbone of the system, linking hundreds of TIMs to a Dynamic Scanning Module. The cable can be used with or without conduit, and T-connectors allow virtually any desired network topology.
When used with appropriate Zener barriers or galvanic isolators, the cable is approved for use in Division 1 and Zone 0 hazardous areas. An innovative aspect of Trendmaster is its ability to support multiple measurement points with a single Galvanic Isolator (or pair of Zener diode barriers) — a feature that dramatically reduces installation costs and simplifies ongoing instrument and grounding system maintenance.
Zener barriers require a high-integrity earth ground connection that needs ongoing maintenance, particularly in environments such as offshore platforms where corrosion is prevalent. Our Galvanic Isolator is preferred when installing in hazardous areas because it eliminates the need for a ground connection altogether by using transformer coupling rather than current-limiting diodes. The result is a safer installation that is less prone to degradation over time and requires no recurring maintenance.
A DSM is the bridge between the Trendmaster TIM lines and the host computer running System 1® software. The DSM communicates with the host computer via Ethernet, over any physical media - standard cabling, fiber-optic, wireless etc… Fiber-optic cable allows signal wiring to be installed in the same conduit as power wiring, without being affected by noise and interference. Wireless Ethernet links avoid this cabling altogether. These options can help minimize installation costs, especially in retrofit situations.
Trendmaster was designed to minimize the bandwidth it requires on existing Ethernet networks within a plant. In almost all cases, Trendmaster can co-exist on existing plant networks rather than requiring its own dedicated network.
Each DSM can accommodate an Ethernet communications card (either wired or fiber-optic) and up to three TIM Input cards. Each TIM input card can accept two TIM lines, with each TIM line supporting a maximum of 254 points* (508 per card). These cards support not only ProTIMs, but also the previous-generation TIMs & FlexiTIMs. Note that TIM input cards can also be referred to as SPA cards, for Signal Processing Adapter.
The TIM input cards perform signal digitization and onboard real-time processing. This processing allows the DSM to return post-processed variables to the System 1 software, reducing the required network bandwidth. The DSM can also return waveforms and spectra as needed. If network connection to system 1 is lost, the DSM continues recording data to internal memory. When connection is re-established, the stored data is transferred to System 1.
* When intrinsically safe barriers are used, the number of TIMs supported will be less for each line. The total number of points supported is a function of cable length and hazardous area classification. Contact your Bently Nevada sales professional or Technical Support for additional information.
So, going back to the title of this article, what is the new software for Trendmaster?
It is of course,System 1 Evo(v20.1之后)。
Trendmaster data was previously acquired using System 1 Classic, then optionally transferred via the “6.X Connector” to System 1 Evo. Today, Trendmaster is natively supported in the latest version of System 1. So today, the full suite of Bently Nevada monitors - from 3500, ADAPT & Orbit 60 protection systems, to Trendmaster, vbOnline Pro, Ranger Pro wireless and SCOUT portables - all feed their condition monitoring data into this one comprehensive plant-wide software platform. System 1’s connectivity to this broad portfolio, and other data systems, along with its strong plotting, alarming, visualization, decision support and diagnostic HMI capabilities position it as a leading solution for all machinery monitoring needs across all industries.
Below are some example screenshots of the implementation in System 1, so you can see for yourself that Trendmaster is comprehensively supported:
Configure the DSM & its cards, and the TIMs/FlexiTIMs/ProTIMs & their channels:
That configuration can be either on-line, while connected to the Trendmaster hardware (as above), or offline, prior to connecting the hardware (as below):
Typical System 1 analysis features like adding trended variables / band alarms are fully supported, along with state-based data collection (e.g. only collect data when the machine is running):
Machine status display includes all the usual formats you have become accustomed to in System 1, including Status List, Bar Graph and Events tables. Similarly, System Health Events for the Trendmaster itself are available under the Devices tab:
And of course, System 1’s powerful charting and trending features are fully applicable to Trendmaster:
Other important software features which are supported include:
- Database migration from 6.x to 20.x including config, data, spectral bands.
- Configuration Download & Upload to/from the DSM.
- Migrate XY channel associations from configuration in S1 Classic, and display Orbit plots.
- Data on Demand, requesting the DSM to immediately measure a particular channel.
- DSM MODBUS Utility, allowing export of Modbus data directly from the DSM.
- Download CM setpoints into DSM for exporting alarm status via Modbus.
- Automated data recording when a Condition Monitoring setpoint is exceeded.
- 获取数据后从DSM的内存establishing a failed network connection.
- DSM Init tool to assist with installing and testing a Trendmaster system.
- Hardware events import and display in System 1.
What system hardware is supported?
Over the Trendmaster system’s ~30 year history, many versions and variants have been produced. System 1 v20+ now supportsnot only the current system, but also the most common obsolete Trendmaster components. Below are the hardware components natively supported by System 1 Evo v20.1
- Network Card: 149776-01 Ethernet 10/100 base T
- Network Card: 149776-02 Fiber Optic
- Signal Processing Adapter (SPA) card: 149787
- 1900/25 Velocity Monitor
- 1900/55 Fan Monitor
- 2300/25 Monitor (configured in System 1 as an RBO ProTIM)
- TIMs(Single channel, 1st generation)
- Displacement
- Key phasor
- Process
- Rack Buffered Output, & Key phasor
- Accel to Velocity
- Velocity
- Temperature, J & K type thermocouples
- FlexiTIMs(Dipswitch addressing, 2 channel, 2nd gen.)
- Accel to Velocity
- Temperature PT100 RTD (100 Ohm Platinum RTD)
- Temperature J TC (J Type Thermocouple)
- Temperature K TC (K Type Thermocouple)
- ProTIMs(Programmable, 2 channel, 3rd generation)
- Accel to Velocity
- Low Frequency Accel to Velocity
- Accel to Velocity with Acceleration Enveloping
- Displacement
- Rack Buffered Output
- Speed Input: Keyphasor
- Temperature: K Type Thermocouple
- Temperature: Platinum RTD (2 & 3 wire, 4 wire coming soon)
- Process Variable
- Pressure
That list is comprehensive; however, it does not cover every obsolete component ever made. Please check with your Bently Nevada sales representative or Technical Support to determine if all the components within your system are supported. If not, two options remain: the 6.X Connector provides a software link to transfer data from your active Classic database for viewing in an Evo database. Or we can help you select from the alternative monitors within the Bently Nevada portfolio which serve a similar purpose, while retaining System 1 connectivity.
Trendmaster has had a long history of making it easy and cost-effective to cover more of your assets with online condition monitoring. This new inclusion into the suite of products supported by System 1 Evo will allow Trendmaster to continue doing so for decades to come. Thus enabling a full plant-wide view into your condition monitoring program.
If you have a Trendmaster system which would benefit from an update to System 1 v20+, or know where a new install would meet some of your condition monitoring needs, we encourage you tovisit our websitefor additional information or contact your nearest Bently Nevada sales professional.
Our Experts
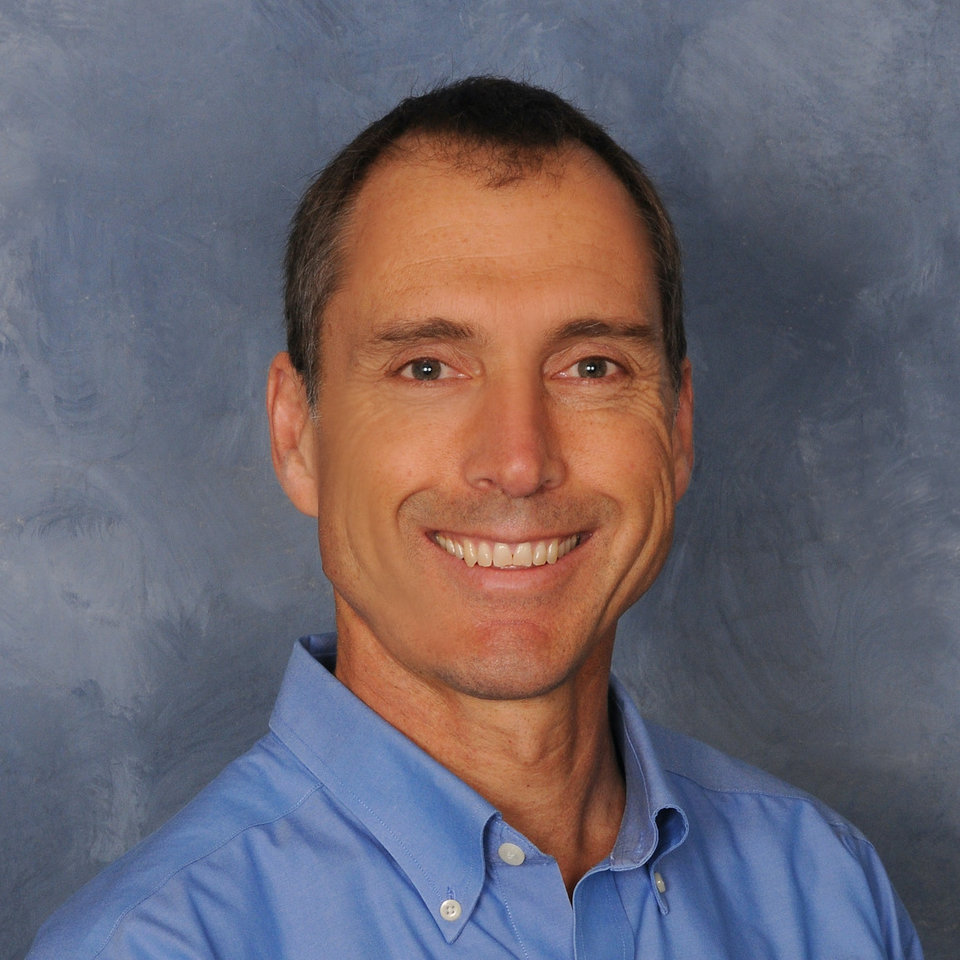
Nigel Leigh
Product Line Manager
BIO
Nigel has 20 years’ experience in the vibration analysis and condition monitoring space, having joined Bently Nevada as part of the Commtest acquisition.