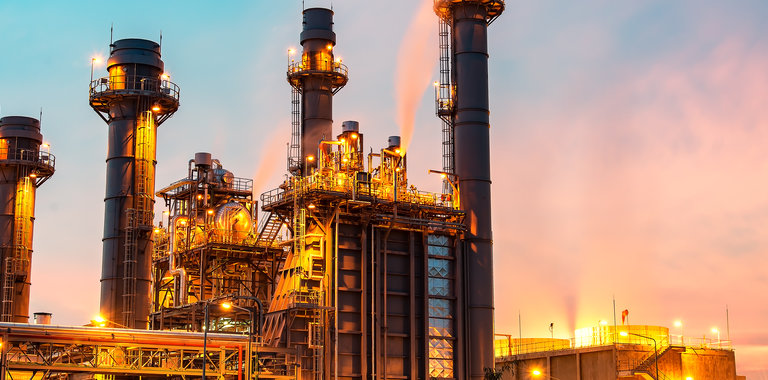
How a Well-trained Workforce Can Reduce Downtime and Operating Costs
According to Energy API, “One out of fourcurrent engineers, geoscientists, multi-skilled maintenance professionals, process and production operators, and health and safety professionals is currently eligible for retirement.”
Oil & gas and power industries are facing a domino effect of workforce challenges.
While this presents a remarkable opportunity forjob growthin the industry – projected to reach 1.3 million through 2030 – it is offset by a very real skills and efficiency gap.Nearly halfof those in the sector recently surveyed believe there is a lack of skilled local workforce.
In an environment that is already cost- and human-resource constrained, this leaves oil & gas and power companies vulnerable to troubling rates of unplanned downtime and maintenance costs. According to a recent ARC Advisory Groupsurvey, companies have been losing between 3-5% of their production to unplanned downtime.
A robust, modern training program can equip personnel with the technical and innovative problem-solving skills needed to prevent unplanned events that can cost millions in lost production and potentially millions in fines.
Employee training and development is big business. According toTrainingmagazine’s most recentTraining Industry Report, training expenditures rose significantly to $90.6 billion in 2017, a 32.5 percent increase. In the oil & gas sector, approximately 25 percent of producers provide internal training and around 20 percent employ external resources, according todatafrom the Society of Petroleum Engineers.
These expenses serve as a wise investment to offset thesignificant costto replace employees, which increases with the level of the employee. While40 percent of employeeswith poor training leave their jobs within the first year, well-trained skilled employees tend to stay put longer.
In a landmarkstudyconducted by the American Society for Training and Development (ASTD), they found an
“increase of $680 in a firm’s training expenditures per employee generates, on average, a six percentage point improvement in total share holder return the following year, even after controlling for many other important factors.”
According toPump and Systems, mechanical issues cause 46 percent of shutdowns, maintenance causes 23 percent, and electrical problems lead to 19 percent. Whatever the reason, it is clear that adequate operations and maintenance training is absolutely vital to keeping power and oil & gas producers operating at peak capacity while keeping downtime costs to a minimum.
Sincenearly 92 percentof maintenance-related shutdowns were unplanned, a well-trained workforce is more equipped to think critically and creatively in the workplace to solve problems and make better decisions on the spot.
The oil & gas and power companies poised to embrace Industry 4.0, are the ones espousing innovation and leading the way with a smarter, better trained workforce. In the cyclical oil industry, it is particularly important to ensure that employees continually keep up with best practices, new skills, and professional development to ensure they remain valuable to the operation.
Did you know that Nexus Controls, a Baker Hughes business, has more than40 years of technical training experience? We have pioneered the art of long-term skill development and are committed to ensuring our customers get the most out of their Industrial Systems and Cybersecurity products. You can learn more about our courses and experience here:
Resources
Type | Name | Language | |
---|---|---|---|
Article |
Nexus Controls Well Trained Workforce Blog |
English |