无损检测(NDT)指广泛的检查或测试方法,允许检验员评估和收集有关材料、部件、焊接、系统或组件的数据,而不会永久地改变或损坏它们。
Waygate技术是全球领先的无损检测产品,用于工业NDT, NDE或NDI检测过程。我们的产品包括最先进的无损检测设备和服务解决方案,为您的射线、涡流、超声波和远程视觉检测任务提供动力。
我们提供最好的检测性能和驱动技术创新,使我们可靠的选择伙伴我们的客户在航空航天,电子,汽车,电池,增材制造和能源行业。
探索我们的投资组合
射线检测-一种无损检测(NDT)-通常使用伽马射线或x射线来检查制造零件的任何缺陷或缺陷,否则视觉检查不会发现。
一种分为两部分的检查方法,射线照相法使用一种发电机顾名思义,它产生的x射线将通过样品,和一个探测器它捕获光线和结果图像以供检查:
- 微焦点x射线管-在真空管中,电子从加热的灯丝中发射出来,并通过电位差UACC向阳极加速。电子通过阳极上的一个孔进入一个磁性透镜,该透镜将电子束聚焦到目标上直径几微米的小光斑上。靶层由沉积在金刚石或轻金属板上的钨薄层组成,也可作为x辐射(传输管)的出口窗口。在钨层中,电子突然减速,从而产生x射线。因此,焦点光点代表一个非常小的x射线源,即使在高倍率下也能实现微米分辨率的最锐成像。最新的纳米聚焦管通过使用多个电子透镜实现了200纳米(0.2微米)的细节可探测性。电子束电流由偏压UG通过Wehnelt电极控制。一组偏转线圈使电子束与透镜的光轴对齐。由于焦点位于离出口窗口外表面0.4毫米的很短的距离,x射线的锥传播了170°的角度。
- 数字探测器阵列-x射线阴影图像由闪烁箔转换为可见光,由光电二极管阵列直接检测到。该技术的主要优点是图像不失真、高动态和高对比度分辨率。最新的温度稳定高动态DXR数字探测器阵列技术确保了高达每秒30帧的精彩实时成像。
工业领域流行的解决方案是便携式,现场准备发电机/探测器解决方案例如那些用于检查的石油天然气管道,以及更大的,实验室和/或生产车间x射线检查和计算机断层扫描(CT)系统如在汽车,航空航天,而且电子产品制造工业,提供了更高的精确度。
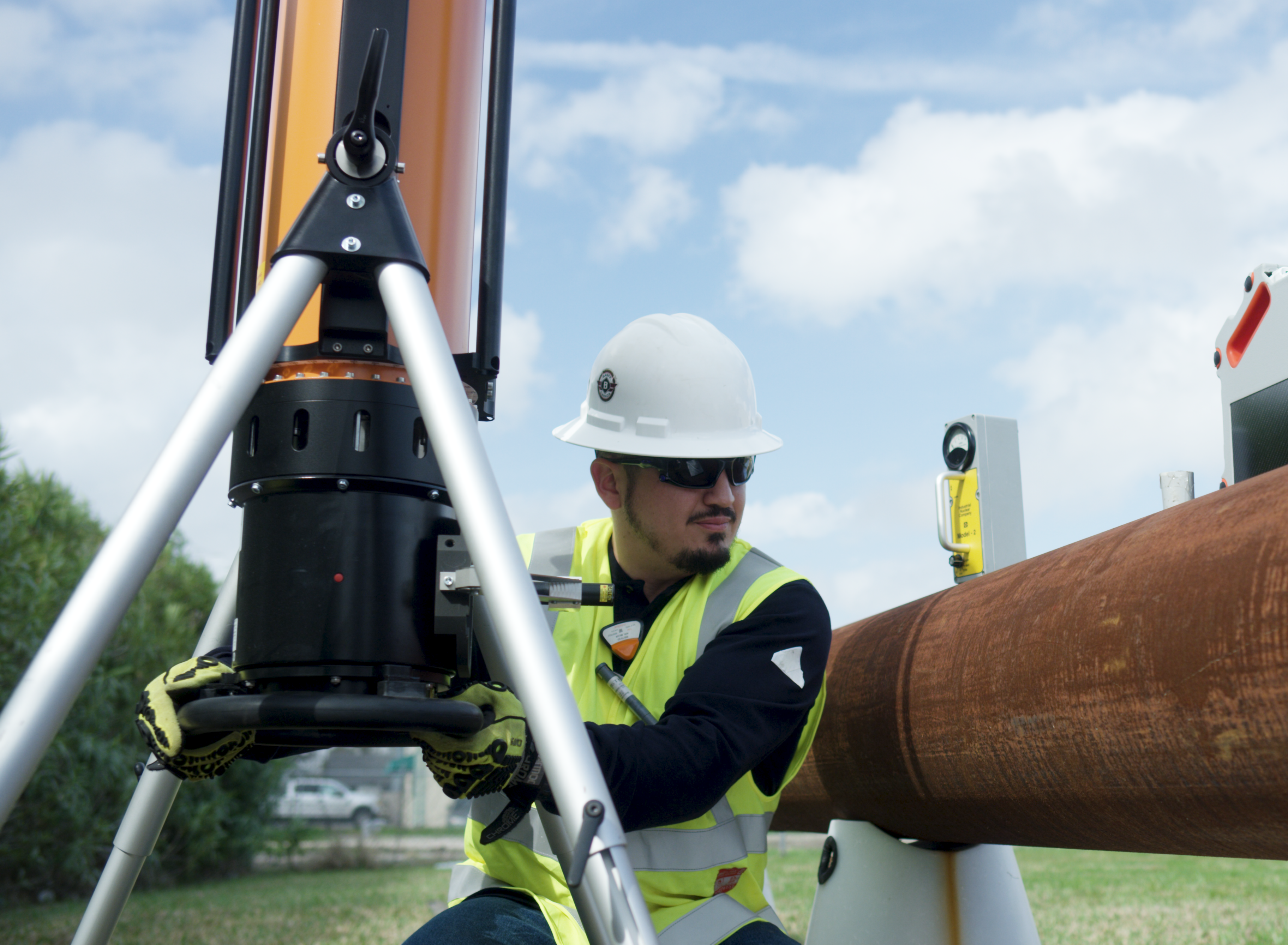
计算机断层扫描是另一种形式的无损检测(NDT)该技术使用数百张x射线图像来创建扫描样本内部和外部结构的三维模型。
有三种与工业CT扫描相关的扫描仪圆锥梁,直线梁,快速龙门螺旋:
- Cone-beam -使用工业锥束CT生成体积数据,首先获取一系列二维x射线图像,同时通过360°旋转逐步旋转样本。这些投影包含了样品中吸收物体特征的位置和密度的信息。这些累积的数据随后被用于体积数据的数值重建。
- 直线束-为了确保高CT数据质量,减少高x射线能量下的散射伪影,准直线探测器阵列被用于CT数据采集。对于每一片切片,通过360°旋转逐步旋转样本,获得一组x射线线轮廓。通过垂直移动样本通过风扇梁和重复这个过程,一组切片被编译,以获得体积的表示。
- 快速龙门螺旋CT在基于医学计算机断层扫描技术的高速螺旋CT中,一个带有x射线管和相应的线探测器的门架围绕在直线带式机械手上转发的工件旋转。为了保证所需的图像质量,缩短测量时间和低散射伪影,使用了高灵敏度的多线检测器。一个典型的铸造工件在10-90秒内被扫描。数值体积重建自动启动,甚至3D评估任务,如自动缺陷识别(3D ADR),包括良好/失败的决策可以完全自动化执行。
CT适合的典型任务包括缺陷检测,计量,失效分析,等等。
现代工业CT解决方案的主要优点之一是能够使用零件与零件或零件与cad的比较其中两个模型被叠加和/或比较:一个是CAD文件或已知好的样品的参考扫描,另一个是正在扫描的生产样品。这种详细程度和参考大大提高了探伤率,并可用于逆向工程和几何尺寸标注。
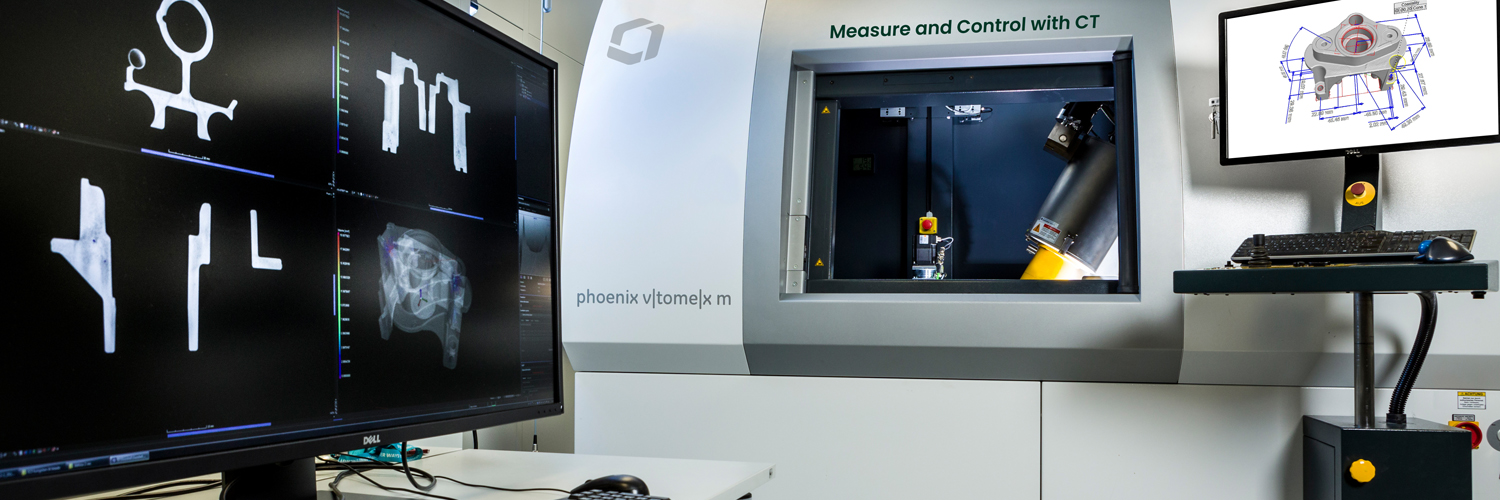
超声波测试(UT)是另一种形式的无损检测(NDT)该技术利用超声波将其传输到材料和样品中,以探测裂缝和撕裂等缺陷,并测量厚度——这是管道焊接、接缝和防腐的一项重要测量方法。
自动超声检测(AUT)指的是UT技术的使用,其中传感器和接收器由一个机械系统驱动,以确保一致的测量以及重复测试的能力。AUT的一个流行应用是在管道检测中,在管道检测中,可以将系统固定在管道的外部,然后沿着管道的长度行走或引导收集数据以进行分析。
相控阵超声检测(PAUT)是一种UT解决方案,它采用一系列相控阵探头,允许光束被聚焦和扫描,而无需物理移动探头——这允许在传统单元件系统可能不适合的更紧凑的位置进行扫描,或在运动受到限制的地方,从而导致更小的扫描尺寸。PAUT是缺陷检测的最佳解决方案之一,在这种情况下,时间是至关重要的,扫描仪的移动性受到损害或不可能,但同时增加了检测概率(POD)。
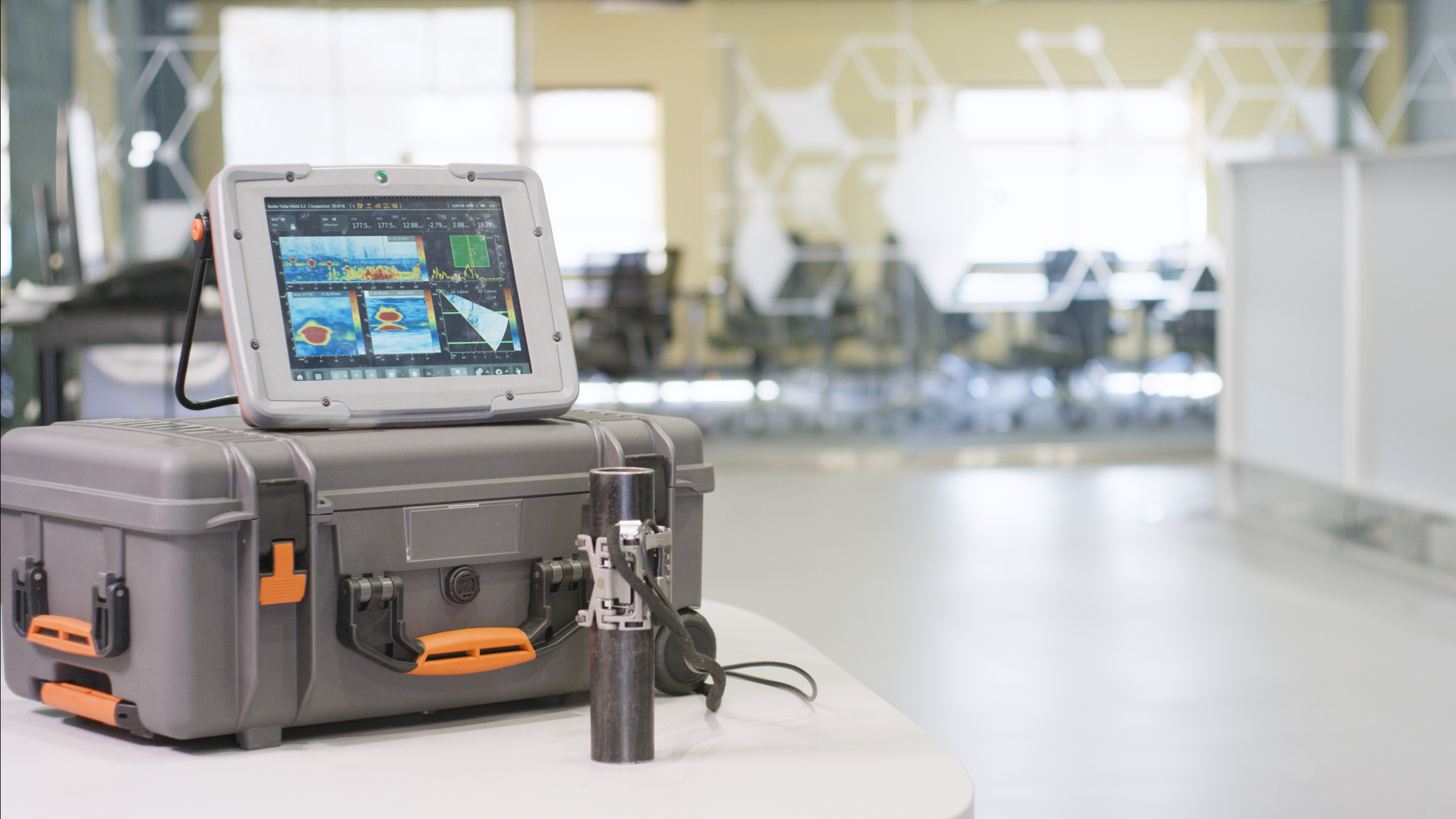
我们广泛的无损检测(NDT)解决方案代表最好的无损检测技术,几乎适用于各行各业的任何应用。
阅读我们下面的任何一个案例研究看看我们如何为您的无损检测项目带来价值。